Siemens Mobility
Siemens Mobility enlisted TXM Consult to address critical operational challenges at its Bogie Service Centre (BSC), which faced a surge in demand. TXM brought its expertise in process optimisation, leadership, and cultural transformation to help the BSC scale production from handling 8 to 30 bogies and 26 to 48 wheelsets weekly.
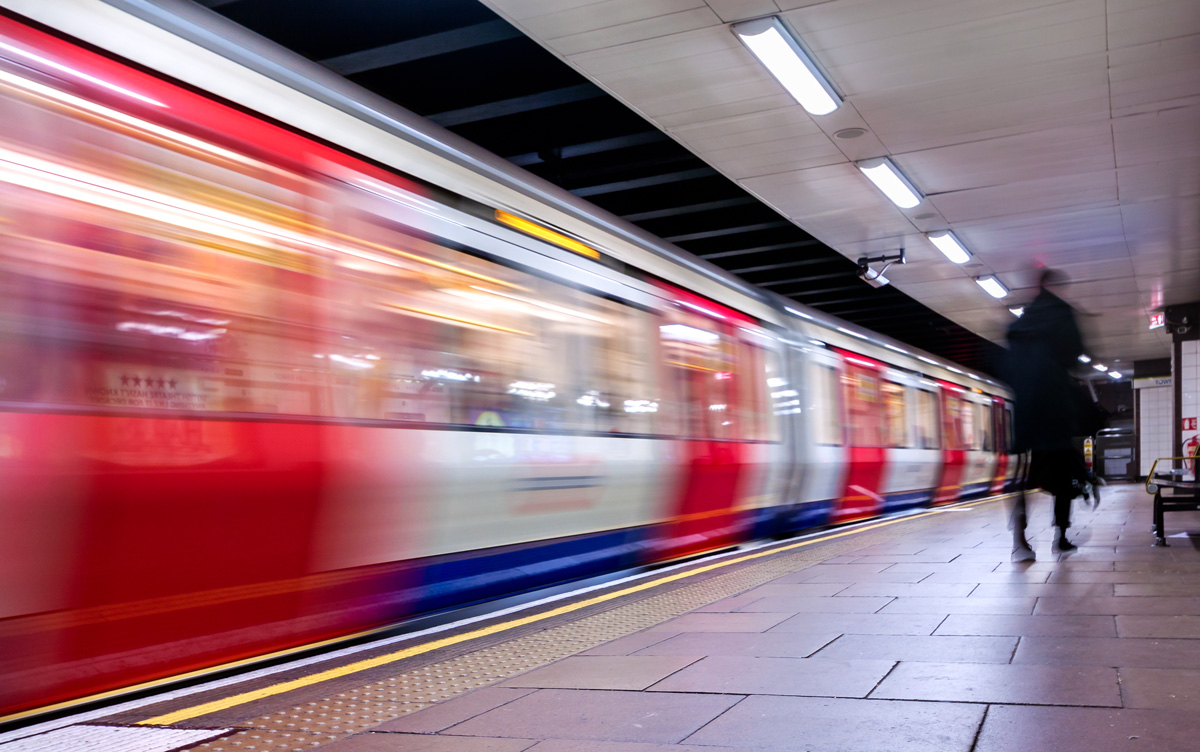
The Challenges
Planning Gaps:
Unrealistic plans overlooked material, capacity, and resource constraints.
Changing Inefficient Processes: :
Bottlenecks and non-value-added activities disrupted workflows.
Limited Collaboration:
Siloed functions and reactive problem-solving limited cohesive teamwork.
The Solutions
Discovery Phase (3 Weeks)
- Reviewed operations and prioritised pain points to create a clear roadmap.
Process Optimisation (3.5 Months)
- Planning: Introduced a 12-month plan, risk mitigation, and user-friendly scheduling tools.
- Production: Mapped workflows, implemented 47 actions (91% completed), and optimised sequencing.
- Culture: Boosted morale with improved leadership presence, reduced meetings, and clear accountability.
Production Oversight (4 Months)
- Embedded improvements into BAU operations, added quality checkpoints, and enhanced.